1. Performance parameters
● Pressure: The maximum pressure required is determined according to actual production needs, which determines the intensity of work that the hydraulic press can complete. For example, the hydraulic press used for stamping in the manufacture of automotive parts needs to calculate the required pressure based on the material, thickness and shape of the stamped parts, which generally ranges from hundreds of tons to thousands of tons.
● Stroke: The stroke length must meet the maximum moving distance required during the workpiece processing. For example, in the metal forging process, the stroke of the hydraulic press needs to be determined according to the height change of the forged part and the forging process requirements to ensure that the forging operation can be completed.
● Speed: The working speed directly affects the production efficiency. For some processes that require fast pressing or return, such as plastic molding, the hydraulic press needs to have a higher speed. At the same time, the stability of the speed is also important to ensure the consistency of the processing quality.
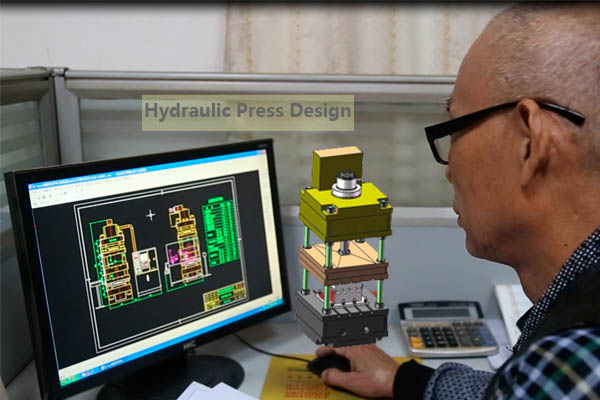
2. Structural design
● Fuse structure: The fuselage should have sufficient strength and rigidity to withstand high pressure and impact loads during operation. Common fuselage structures include frame type, four-column type, etc. The frame type has good rigidity and is suitable for large hydraulic presses; the four-column type has high guiding accuracy and is easy to install and operate.
● Workbench size: Determine the workbench size according to the size of the workpiece and the production process requirements to ensure that the workpiece can be stably placed and processed on the workbench. For example, for a hydraulic press that processes large molds, the workbench size must be large enough to accommodate the mold and leave a certain amount of operating space.
● Mold installation method: Reasonably design the mold installation method to facilitate rapid clamping and positioning of the mold and improve production efficiency. Common installation methods include bolt connection, pressure plate fixation, etc., which can be selected according to the structure and use requirements of the mold.
3. Control System
● Hydraulic system: A hydraulic system is a technology that uses pressurized fluid to transmit power and perform mechanical work. It is based on Pascal's Law, which states that pressure applied to a confined fluid is transmitted equally in all directions. Hydraulic systems are widely used in various industries due to their ability to generate high force with precise control. Hydraulic system include oil pump, hydraulic cylinder and hydraulic value.
● Automation degree: Determine the automation degree of the hydraulic press according to production needs, such as manual control, semi-automatic control or fully automatic control. Fully automatic control can improve production efficiency and processing accuracy and reduce manual operation errors, but the cost is relatively high.
● Control accuracy: For some processes that require high processing accuracy, such as precision forging, powder metallurgy, etc., the control system needs to have high control accuracy to achieve accurate control of parameters such as pressure, stroke and speed.
● Human-machine interface: A good human-machine interface should be easy and intuitive to operate, making it easy for operators to set parameters, monitor equipment operating status and diagnose faults. For example, a touch screen interface can provide a graphical operation interface to facilitate operators to perform various operations.
● Automation degree: Determine the automation degree of the hydraulic press according to production needs, such as manual control, semi-automatic control or fully automatic control. Fully automatic control can improve production efficiency and processing accuracy and reduce manual operation errors, but the cost is relatively high.
● Control accuracy: For some processes that require high processing accuracy, such as precision forging, powder metallurgy, etc., the control system needs to have high control accuracy to achieve accurate control of parameters such as pressure, stroke and speed.
● Human-machine interface: A good human-machine interface should be easy and intuitive to operate, making it easy for operators to set parameters, monitor equipment operating status and diagnose faults. For example, a touch screen interface can provide a graphical operation interface to facilitate operators to perform various operations.
Hydraulic Press solution manufacturer - Delishi/Goodsjack Hydraulic Machinery is specializing in hydraulic press designing and manufacturing nearly 30 years experience. If you need hydraulic machine and want to get the best hydraulic press design, please contact us.